Unlocking Efficiency: The Importance of Pump Station Monitoring
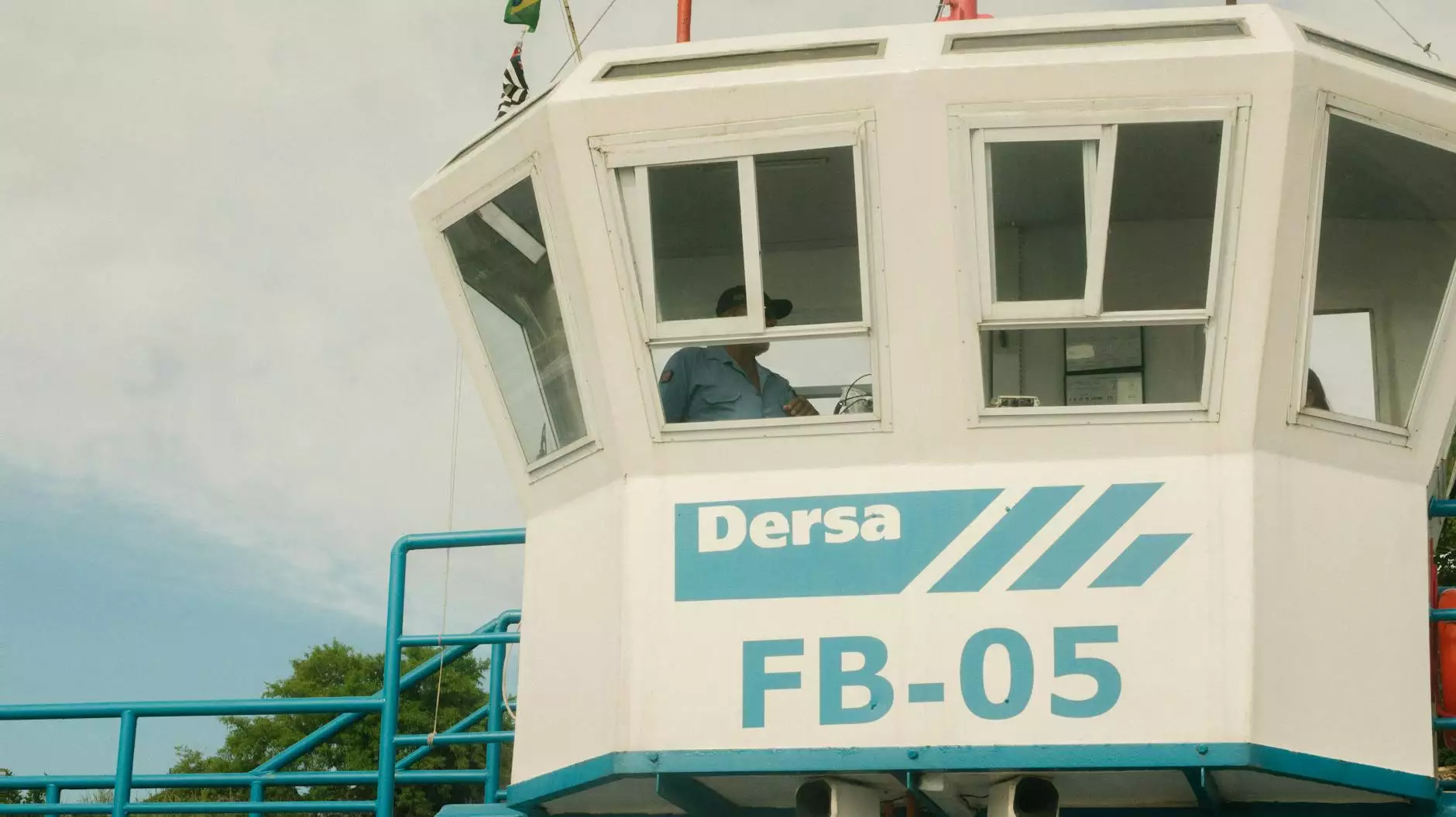
In today’s rapidly evolving industrial landscape, pump station monitoring has emerged as a crucial element for businesses specializing in Auto Parts & Supplies and Safety Equipment. By leveraging advanced monitoring technologies, companies can enhance productivity, ensure safety compliance, and drive down operational costs. This comprehensive guide delves into the significance of pump station monitoring and its multifaceted benefits, highlighting how it contributes to superior business performance.
What is Pump Station Monitoring?
Pump station monitoring refers to the systematic process of overseeing the operation and condition of pump stations used in industrial applications. These monitoring systems collect data on various parameters, including:
- Flow Rates: Measurement of fluid movement.
- Pressure Levels: Assessment of pressure systems to prevent failures.
- Temperature: Monitoring of temperature output to ensure optimal operations.
- Vibration Analysis: Detection of abnormal vibrations which may indicate malfunction.
- Power Consumption: Evaluation of energy use for efficiency improvements.
By utilizing these metrics, businesses can gain insights into the performance and health of their pumping systems, paving the way for timely maintenance, operational improvements, and cost efficiency.
Why is Pump Station Monitoring Essential?
The value of pump station monitoring cannot be overstated. Let’s explore several compelling reasons why incorporating these monitoring systems is essential for organizations:
1. Enhanced Operational Efficiency
Implementing a pump station monitoring system allows businesses to optimize their operations. By continuously tracking pump performance, companies can identify inefficiencies, adjust operational strategies, and reduce downtime. This results in streamlined processes and maximized productivity.
2. Cost Savings
With precise data collection, organizations can significantly lower their operational costs. Here’s how:
- Preventive Maintenance: Early detection of issues leads to timely maintenance, avoiding costly repairs and replacements.
- Energy Efficiency: Monitoring power consumption reduces energy waste, directly impacting the bottom line.
- Asset Longevity: Proper care keeps equipment in good condition longer, thereby extending its lifespan and reducing capital expenditure.
3. Safety Compliance
In industries where pump stations are pivotal, safety is paramount. Monitoring systems ensure that all operations adhere to safety regulations by:
- Real-time Alerts: Instant notifications about abnormal conditions help prevent accidents.
- Regulatory Compliance: Consistent data records facilitate compliance with industry regulations.
4. Improved Decision-Making
With real-time data at their fingertips, business leaders can make informed decisions. Accurate analytics on pump performance enable organizations to:
- Strategize Resource Allocation: Understanding system performance helps allocate resources effectively.
- Plan Capacity Improvements: Data-driven insights facilitate better planning for future needs.
Technological Advances in Pump Station Monitoring
The advent of cutting-edge technology has revolutionized pump station monitoring. Modern systems employ a variety of tools and methods that enhance monitoring capabilities:
1. IoT Sensors and Devices
The Internet of Things (IoT) has introduced smart sensors that collect real-time data from pump stations. These sensors can communicate with centralized databases, providing accurate information on system performance. The benefits include:
- Remote Monitoring: Access data from anywhere, allowing for prompt action without physical inspections.
- Automated Reporting: Generates reports automatically, saving time and resources.
2. Cloud Computing
Cloud-based systems offer scalable and accessible solutions for data storage and analysis. By incorporating cloud technology, businesses can:
- Store Large Data Sets: Save extensive data without investing in physical storage.
- Access Data Anytime: Utilize data from various locations and devices.
3. Data Analytics and AI
Utilizing data analytics and artificial intelligence further enhances the ability to monitor and analyze pump operations. This technology enables the following:
- Predictive Maintenance: Algorithms predict potential issues before they arise, optimizing maintenance schedules.
- Performance Optimization: Provides insights into improving system efficiency based on historical data trends.