Understanding Plastics Injection Mold: A Key to Modern Manufacturing
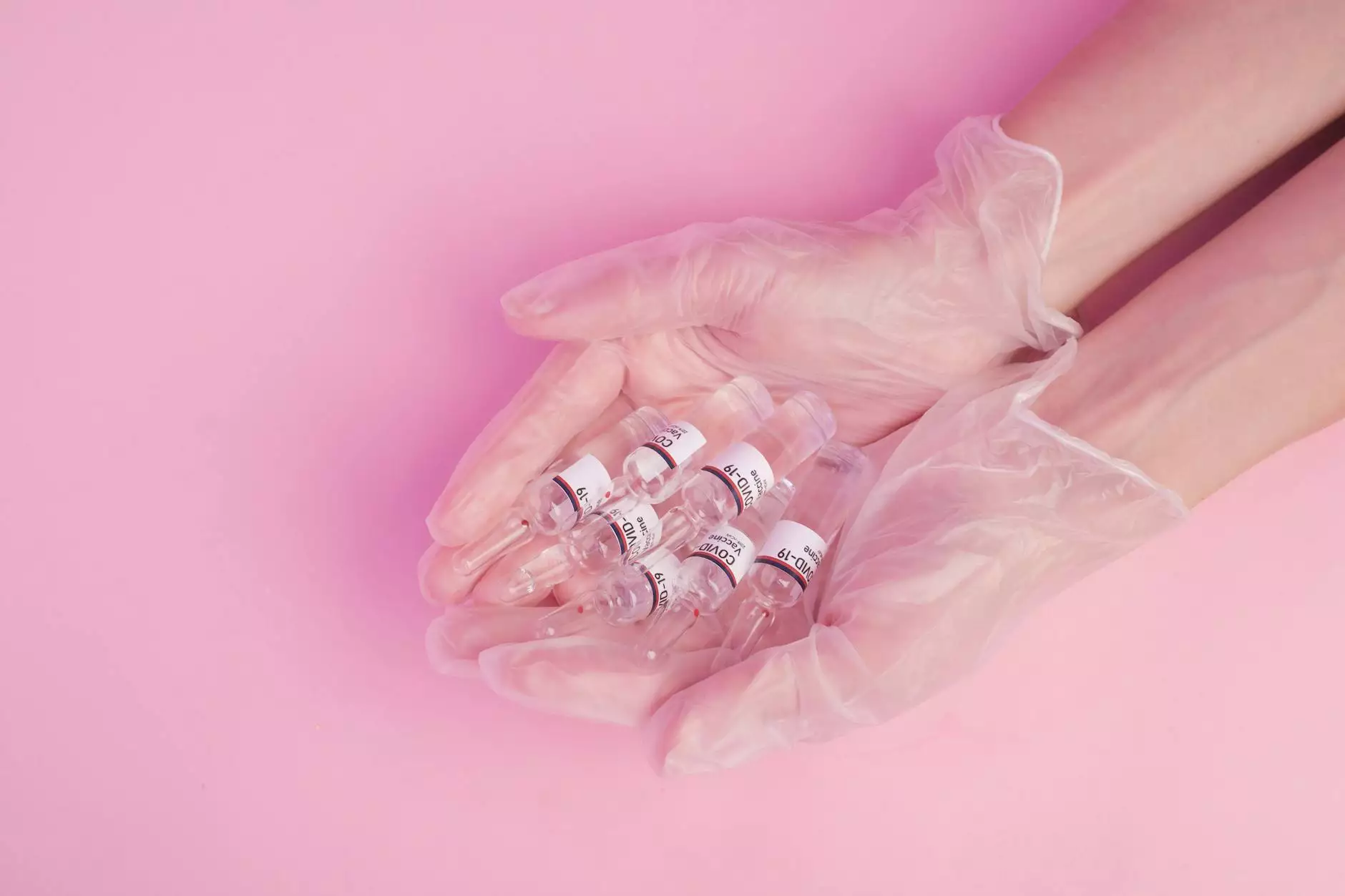
Plastics injection mold is a revolutionary technique that has transformed the manufacturing landscape across various industries. This process not only facilitates the production of complex plastic parts but also significantly enhances efficiency and cost-effectiveness. In this article, we will delve deep into the intricacies of plastics injection molding, exploring its processes, benefits, applications, and future trends.
What is Plastics Injection Molding?
The plastics injection mold process involves a series of steps where molten plastic material is injected into a precisely designed mold cavity. The mold is cooled, solidifying the plastic into the desired shape. This method is renowned for its ability to produce a high volume of identical parts with remarkable precision and speed.
The Injection Molding Process
- Material Selection: The first step is choosing the appropriate plastic material, which can vary depending on the application. Common options include ABS, polycarbonate, and polyamide.
- Designing the Mold: Expert engineers design a mold that encompasses the desired part's specifications, ensuring functionality and aesthetics.
- Injection: The chosen plastic is heated until it becomes molten and is then injected into the mold under high pressure.
- Cooling: Once injected, the plastic remains in the mold for a set cooling period to solidify.
- Removal: After cooling, the mold opens, and the finished part is ejected, ready for use.
Advantages of Plastics Injection Molding
The plastics injection mold technique stands out in manufacturing due to its multiple advantages:
- High Efficiency: The ability to produce thousands of parts in a short time makes this method incredibly efficient for high-volume production.
- Cost-Effectiveness: While the initial setup cost is higher, the per-unit cost decreases significantly with increased production, making it economical for large batches.
- Complex Geometries: Injection molding allows for the creation of intricate designs that would be challenging or impossible with other manufacturing methods.
- Consistent Quality: The automated nature of the process ensures that each product is produced with high precision and uniform quality.
- Versatility: Various materials can be used, including thermoplastics and thermosetting plastics, catering to diverse industry needs.
Applications of Plastics Injection Molding
From consumer goods to automotive parts, the applications of plastics injection mold are vast. Here are some critical areas where this technique shines:
1. Automotive Industry
The automotive sector extensively uses injection molding to manufacture parts such as dashboards, door panels, and switches. The lightweight nature of plastics combined with the durability of molded parts contributes to fuel efficiency and vehicle performance.
2. Consumer Electronics
In consumer electronics, injection molding is critical for producing cases and components of devices. The precision offered by plastics injection mold helps in the snug fit of parts, ensuring high-quality end products.
3. Medical Devices
In healthcare, the need for sterile and precisely engineered devices has led to the adoption of injection molding for creating items like syringes, tubing, and surgical tools.
4. Packaging
Injection molded plastics are widely used in producing packaging materials that are not only functional but also sustainable, such as biodegradable containers.
Future Trends in Plastics Injection Molding
The landscape of plastics injection mold is continually evolving. Here are some anticipated trends:
1. Sustainability Focus
With an increasing emphasis on sustainability, manufacturers are leaning towards biodegradable plastics and recycling processes that reduce waste and environmental impact.
2. Advanced Technology Integration
New technologies such as 3D printing and automation are set to revolutionize the injection molding process, improving efficiency and reducing production times.
3. Customization and Flexibility
As consumer demands shift towards personalized products, injection molding will adapt by enabling shorter runs and customized designs without compromising quality.
Deepmould.net: Your Partner in Injection Molding Solutions
At Deepmould.net, we specialize in offering top-tier plastics injection mold solutions tailored to your business needs. Our state-of-the-art facility and experienced team ensure that we deliver precision-engineered products that align perfectly with your specifications.
Why Choose Deepmould.net?
- Expertise: Our dedicated team brings years of experience in creating high-quality injection-molded products.
- Customization: We work closely with our clients to understand their specific requirements and adapt our services accordingly.
- Quality Control: With rigorous quality control processes in place, we ensure that our products meet industry standards and client expectations.
- Comprehensive Services: From design to production and post-processing, our complete range of services supports all aspects of the injection molding process.
Conclusion
The plastics injection mold techniques have revolutionized the manufacturing industry through their efficiency, cost-effectiveness, and ability to produce complex parts. As we move forward, embracing sustainability and advanced technologies will be key to harnessing the full potential of this innovative process. Whether in automotive, medical, or consumer goods, injection molding will continue to play a vital role in meeting the diverse needs of modern manufacturing.
If you are considering incorporating plastics injection mold into your production processes, reach out to us at Deepmould.net to discuss how we can help you achieve your goals with our expert solutions.